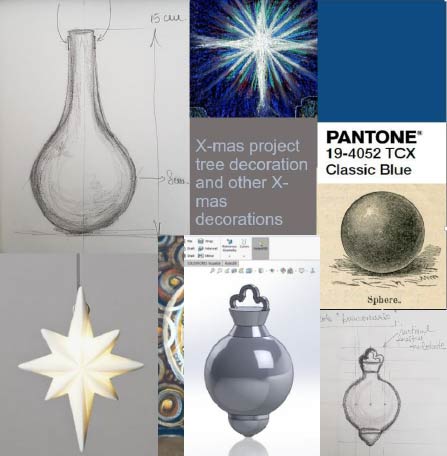
Materials used: porcelain, GUS 33, paper clay. Procedures: Split casting in plaster molds, modeling, hand build, potter's wheel. All images on objects are hand-painted, giving uniqueness to each product. All products are handcrafted with attention to detail, respecting the environment by using lead-free non-toxic food glazes, but also by responsible waste management. Both the process and the materials give value to the product. If the basic materials are the same every time, they end up being enlivened by the process and the results will be different, being influenced by the feeling, thinking and skill of the one who uses them. Design process Irrespective of whether they are created by using slip casting technique, or by modeling or using the potter's wheel, each object or collection is based on a long design process. I have in mind different sources of inspiration (books, internet magazines), the environment (color of the moist soil, leaves moved by the wind, plumage of the birds, color of the flowers in the meadows), but especially the stories with their fantastic symbols, myths and characters. All these pieces of information, thoughts and feelings are merged into sketches that then become plaster molds for future shapes, suggestions for decorating objects.
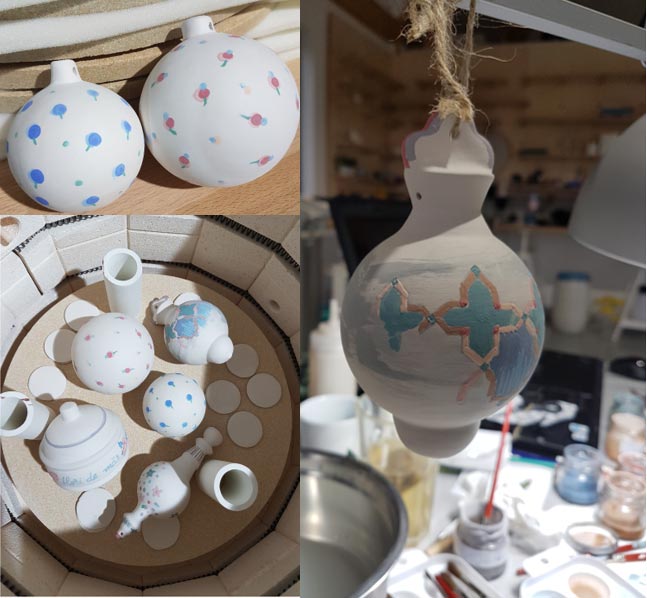
Decorating and firing at 900 degrees Celsius Once the objects removed from the mold have dried, be it shaped or made on the potter's wheel, I decorate them with pigments if I want to decorate under the glaze and then place them in the oven for the first firing, also called biscuit. The drying time is influenced by the type of material used, the size of the objects, the temperature and humidity conditions from studio. In this phase the objects can touch each other. The firing program lasts a few hours, the maximum temperature is 900 degrees Celsius. After the program ends I have to wait at least 8 hours for the oven temperature to drop to at least 100 degrees Celsius. Only after this waiting time I can open the oven.
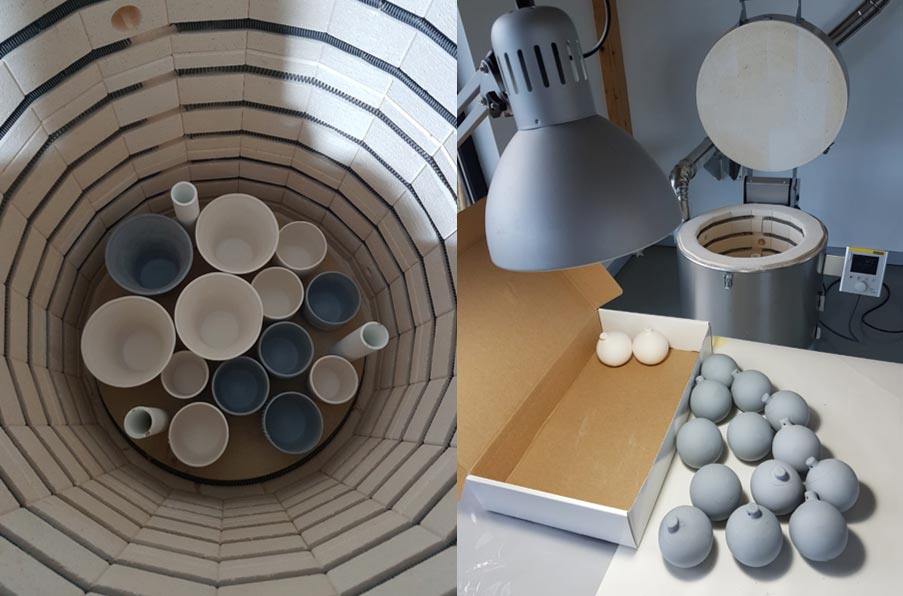
Glazing and firing at 1250 degrees Celsius I must admit that the glazing process is the one that gives the final value to the object. It is a process that requires a lot of attention, skill, patience, experience gained through continuous exercise. After the first firing I clean the objects of the firing residues, wash or wipe some with a damp sponge, let them dry and then start in the morning, because I noticed that the best glaze it is done in natural light, I start the glazing process. After immersing the objects in the glaze, I let them dry and then retouch them in such a way that the glaze evenly covers the entire surface. There is a lot to tell, there are all kinds of techniques, but in the end, each potter finds his own methods depending on the shape, size of objects, types of glazes used, techniques applied and the effects he wants to achieve in the end. … Because at this stage things are not what they seem, the glazes has transforming at high temperatures and form a common body with the porcelain, they change on the face, some are chameleon-like. Surprises often appear after you open the oven, even after many years of practice. At the second firing to 1250 Celsius degree, the objects shouldn’t touch each other or touch the oven plate if the base is glazed. To avoid accidental gluing of objects to each other, or to the oven plate, I apply all sorts of solutions, supports, Kanthal wires and others… a whole universe of little secrets stolen from others or discovered along the way. It is the longest process, lasts about 33 hours from the start of the firing program at 1250 degrees Celsius and until cooling.
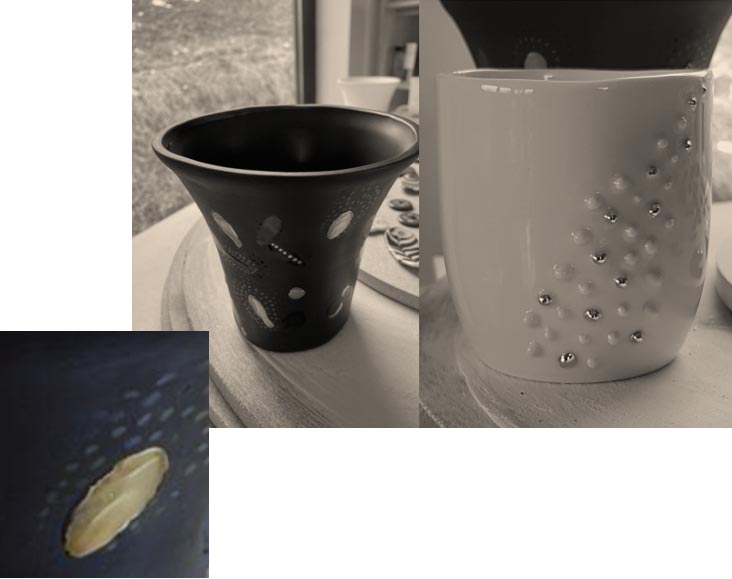
Sometimes the third firing happens, decor firing at 750-800 degrees Celsius. If I want to decorate over the glaze with decorative colors or with lusters or preparations made of precious metals, then, after the second firing, when the glaze sits nicely over the objects and gives them a protective layer, I decorate them and then, after drying, I put them in oven for the third firing. I do this operation only when I want to put some gold or platinum accents. If I want the effect to be matte, I apply it over a matte glaze, and if I want the gold to shine like the sun, I apply it over a glossy glaze.